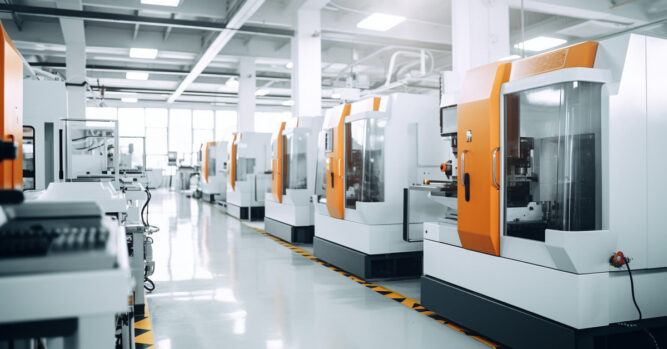
Step inside the dynamic world of modern machine shops, where precision meets innovation, and craftsmanship intertwines with cutting-edge technology. In this article, we will unravel the secrets behind mastering precision in machining processes, unlocking the key to unparalleled quality and efficiency. From state-of-the-art equipment to advanced techniques, we delve into the core elements that propel machine shops into the forefront of industrial excellence.
Experience the intricate dance of man and machine as they work in harmony to fabricate intricate components with flawless accuracy. Discover how meticulous planning, skilled labor, and automation converge to push the boundaries of what is possible in the realm of manufacturing. Whether you are a seasoned industry professional or an aspiring enthusiast, this deep dive into the world of modern machine shops promises to enlighten and inspire, offering a glimpse into the future of precision engineering.
Understanding Modern Machine Shops
Modern machine shops are a fascinating blend of traditional craftsmanship and advanced technology, creating an environment where precision and efficiency are paramount. At their core, machine shops are facilities where various components and parts are manufactured through processes such as cutting, shaping, and assembling materials. These shops cater to a wide range of industries, including aerospace, automotive, and medical, producing everything from simple brackets to complex engine components. The capabilities of modern machine shops extend beyond mere fabrication; they embody a comprehensive ecosystem that incorporates design, engineering, and quality control to ensure unparalleled accuracy and performance.
The layout and organization of a modern machine shop play a crucial role in its operational efficiency. A well-designed machine shop optimizes workflow, minimizes waste, and enhances productivity. This is achieved through strategic placement of machinery, tools, and workstations, allowing for a seamless transition from one stage of production to another. Additionally, modern machine shops often employ lean manufacturing principles, focusing on reducing cycle times and eliminating non-value-added activities. By fostering a culture of continuous improvement, these shops can adapt to changing demands and maintain a competitive edge in the marketplace.
Furthermore, the workforce in modern machine shops is a vital asset, blending skilled labor with technological proficiency. Operators and machinists must possess a deep understanding of machining processes, materials, and equipment to produce high-quality components consistently. As technology advances, the importance of continuous training and education becomes evident, ensuring that employees remain adept in the latest techniques and tools. This synergy between human expertise and technological advancement is what defines the success of modern machine shops in an ever-evolving industrial landscape.
Evolution of Precision Machining
The evolution of precision machining has been marked by significant technological advancements and changes in manufacturing practices. Historically, machining processes were labor-intensive, relying heavily on manual operations to shape materials. However, the introduction of automated machinery in the mid-20th century revolutionized the industry, enabling higher accuracy and efficiency. The shift from manual to automated machining laid the groundwork for modern practices, where computer numerically controlled (CNC) machines dominate the landscape, allowing for complex geometries and tighter tolerances that were previously unattainable.
As technology progressed, materials science also advanced, leading to the development of high-performance alloys and composites. These materials require specialized machining techniques and equipment, further driving innovation in the field. The integration of computer-aided design (CAD) and computer-aided manufacturing (CAM) software has streamlined the design-to-production process, enabling engineers and machinists to collaborate more effectively. This evolution not only enhances the precision of machined parts but also reduces lead times and costs, making it possible to produce intricate components on a larger scale.
Today, precision machining is characterized by its focus on quality and sustainability. Modern machine shops are increasingly adopting practices that minimize waste and energy consumption, aligning with global efforts to promote environmental responsibility. Additionally, the rise of Industry 4.0 has introduced concepts such as the Internet of Things (IoT) and big data analytics into machining processes, allowing for real-time monitoring and predictive maintenance. This evolution signifies a shift towards smarter manufacturing, where precision is not merely a goal but an integral part of the manufacturing ecosystem.
Importance of Precision in Manufacturing
Precision plays a critical role in manufacturing, impacting everything from product quality to operational efficiency. In industries like aerospace and medical, where safety and reliability are paramount, even the slightest deviation from specifications can have catastrophic consequences. Precision machining ensures that components fit together seamlessly, function correctly, and meet stringent regulatory standards. As a result, manufacturers that prioritize precision gain a competitive advantage, establishing themselves as leaders in their respective fields.
Moreover, the demand for high-quality products continues to rise as consumers become more discerning. Industries are increasingly tasked with delivering not only functional components but also aesthetically pleasing designs that meet exacting standards. Precision machining allows manufacturers to achieve intricate designs and finishes that enhance the overall product appeal. This emphasis on detail and quality has led companies to invest in advanced technologies and skilled labor, recognizing that precision is not just a technical requirement but a market differentiator.
In addition to quality, precision also contributes to cost savings and efficiency. By reducing scrap rates and rework, manufacturers can optimize their production processes and minimize waste. Precision machining enables more accurate forecasting and inventory management, helping companies maintain lean operations. Ultimately, precision is not just about creating perfect parts; it is about driving overall business success by improving product quality, enhancing customer satisfaction, and increasing profitability.
Technologies Shaping Modern Machine Shops
The landscape of modern machine shops is continuously evolving, driven by technological advancements that enhance precision, efficiency, and productivity. One of the most transformative technologies is CNC machining, which utilizes computer-controlled tools to automate machining processes. This innovation allows for high precision and repeatability, making it possible to produce complex parts with minimal human intervention. CNC machines are equipped with advanced software that can interpret intricate designs, ensuring that each part is manufactured to exact specifications.
Another significant technology shaping modern machine shops is additive manufacturing, commonly known as 3D printing. This method allows for the creation of components layer by layer, offering unparalleled design flexibility. Additive manufacturing is particularly advantageous for producing prototypes and low-volume production runs, as it reduces lead times and material waste. While traditionally used for plastics, advancements in metal 3D printing are expanding its applicability to industries that require high-strength, lightweight components.
Furthermore, the integration of IoT and smart technologies is revolutionizing the way machine shops operate. By connecting machines and systems to the internet, manufacturers can monitor performance in real-time, enabling predictive maintenance and minimizing downtime. Data analytics tools allow machine shops to analyze production metrics, identify bottlenecks, and implement targeted improvements. This data-driven approach enhances decision-making and leads to more efficient operations, ultimately contributing to the overall success of modern manufacturing environments.
Key Components of a Modern Machine Shop
A modern machine shop is comprised of several key components that work in concert to achieve precision manufacturing. First and foremost is the machinery itself, which includes CNC mills, lathes, and grinders. These machines are the backbone of the shop, responsible for executing the complex cutting and shaping processes necessary to create high-quality components. Each machine is equipped with specialized tools designed for specific tasks, allowing for a wide range of operations from simple to highly intricate.
In addition to machinery, modern machine shops require advanced software systems for design and production management. CAD software is essential for creating detailed designs and schematics, while CAM software translates these designs into machine-readable code. This seamless integration between design and manufacturing is crucial for maintaining precision throughout the production process. Furthermore, enterprise resource planning (ERP) systems help manage inventory, scheduling, and workflow, ensuring that operations run smoothly and efficiently.
Quality control is another critical component of modern machine shops. Implementing rigorous inspection and testing protocols is vital to ensuring that each part meets the required specifications. This involves using advanced measuring tools, such as coordinate measuring machines (CMMs) and laser scanners, to assess dimensions and tolerances accurately. Quality assurance processes not only help to identify defects early in the production cycle but also foster a culture of continuous improvement, where feedback is used to refine processes and enhance overall quality.
Precision Tools and Equipment
The tools and equipment used in modern machine shops are essential for achieving the high levels of precision required in today’s manufacturing environment. Cutting tools, such as end mills, drills, and inserts, are designed with specific geometries and coatings to optimize performance and extend tool life. Material selection for these tools is critical, as they must withstand high temperatures and wear while maintaining sharpness and dimensional accuracy. Advances in materials science have led to the development of high-speed steels and carbide tools that significantly enhance machining efficiency.
In addition to traditional cutting tools, modern machine shops utilize various specialized equipment to enhance precision and efficiency. Tool holders, collets, and fixtures play a crucial role in securing workpieces and ensuring accurate positioning during machining operations. Innovative clamping systems have been developed to minimize vibration and movement, which can negatively impact precision. Furthermore, the use of automated tool changers allows for quick adjustments between different machining operations, streamlining production and reducing cycle times.
Measuring and inspection tools are equally important in a precision machining environment. Instruments such as micrometers, calipers, and optical comparators are used to verify that machined parts meet stringent specifications. Additionally, non-destructive testing (NDT) methods, such as ultrasonic and X-ray inspection, are employed to assess the integrity of components without compromising their functionality. These tools and techniques ensure that every part produced in a modern machine shop adheres to the highest quality standards, reinforcing the commitment to precision manufacturing.
Innovations in CNC Machining
CNC machining has seen remarkable innovations that have reshaped the landscape of modern manufacturing. One of the most significant advancements is the development of multi-axis machining centers. Traditional CNC machines typically operate on three axes, but modern multi-axis machines can work on five or even six axes simultaneously. This capability allows for the production of highly complex geometries and intricate features in a single setup, significantly reducing production time and improving precision.
Another noteworthy innovation in CNC machining is the integration of advanced sensors and feedback systems. These technologies enable real-time monitoring of machining processes, allowing operators to detect anomalies and make immediate adjustments. This level of oversight enhances the overall quality of machined parts and reduces the risk of defects. Additionally, the use of adaptive machining strategies, where the CNC system adjusts cutting parameters based on real-time feedback, further optimizes performance and extends tool life.
Furthermore, software advancements have dramatically improved the programming and simulation of CNC operations. Modern CAM software includes sophisticated simulation capabilities that allow machinists to visualize the machining process before any physical cutting occurs. This proactive approach helps identify potential issues, such as tool collisions or inefficient tool paths, before they become costly problems. As CNC technology continues to evolve, these innovations are paving the way for even greater levels of precision and efficiency in modern machine shops.
Skills Required for Precision Machining
The field of precision machining demands a diverse set of skills that combine technical knowledge with practical experience. First and foremost, machinists must possess a strong understanding of machining principles and processes. This includes knowledge of various materials, cutting techniques, and machining tools. A solid foundation in mathematics is also essential, as precision machining requires accurate calculations for dimensions, tolerances, and feeds and speeds.
Additionally, proficiency in operating and programming CNC machines is critical in modern machine shops. Machinists must be able to read and interpret technical drawings and blueprints, translating them into machine code that guides the machining process. Familiarity with CAD and CAM software is increasingly important, as these tools streamline the design and manufacturing workflow. Continuous training and skill development are vital, as technology and machining processes evolve rapidly, necessitating ongoing education to stay competitive.
Moreover, attention to detail and problem-solving skills are indispensable in precision machining. Machinists must be able to identify and diagnose issues that arise during production, implementing effective solutions to maintain quality and efficiency. Strong communication skills are also essential, as machinists often work in teams, collaborating with engineers and quality control personnel to ensure that production goals are met. The combination of these skills creates a workforce capable of mastering precision in modern machine shops, driving success in the manufacturing industry.
Industry Applications of Modern Machine Shops
Modern machine shops serve a multitude of industries, each with unique requirements and challenges. In the aerospace sector, precision machining is critical for the production of components that must withstand extreme conditions, such as high temperatures and pressures. Parts like turbine blades, landing gear, and structural components demand unparalleled accuracy and reliability, as they play a vital role in ensuring the safety and performance of aircraft. Advanced machining techniques and materials are employed to meet the rigorous standards set by regulatory bodies in this field.
The automotive industry is another significant sector that relies heavily on precision machining. From engine components to transmission parts, the demand for high-quality, precise components is ever-growing. As vehicles become more complex, with advancements in electric and autonomous technologies, the need for innovative machining solutions intensifies. Modern machine shops produce everything from intricate fuel injectors to robust chassis components, ensuring that every part functions seamlessly within the vehicle’s intricate systems.
Additionally, the medical industry has increasingly turned to modern machine shops for precision manufacturing. Medical devices and components, such as surgical instruments, implants, and diagnostic equipment, require stringent adherence to quality and precision standards. The use of biocompatible materials and advanced machining techniques ensures that these components are not only precise but also safe for patient use. As the demand for customized medical solutions grows, modern machine shops are well-equipped to adapt to these evolving needs, providing tailored solutions that enhance patient outcomes.
Conclusion: The Future of Precision Manufacturing
The future of precision manufacturing is poised for exciting advancements as technology continues to evolve. As modern machine shops embrace automation and smart manufacturing practices, the potential for increased efficiency and precision is limitless. The integration of artificial intelligence and machine learning into machining processes will further enhance decision-making and optimize production workflows. These technologies will enable machine shops to anticipate maintenance needs, reduce downtime, and improve overall operational efficiency.
Sustainability will also play a crucial role in the future of precision manufacturing. As industries strive to reduce their environmental impact, modern machine shops will need to adopt practices that minimize waste and energy consumption. Innovations in materials, such as biodegradable composites and recycled metals, will become increasingly important. By prioritizing sustainable practices, machine shops can contribute to a greener future while maintaining their commitment to quality and precision.
Ultimately, the future of precision manufacturing hinges on the ability to adapt and innovate. As global markets continue to evolve, modern machine shops must remain agile, embracing new technologies and methodologies to meet the changing demands of various industries. By fostering a culture of continuous improvement and investing in the workforce, machine shops can position themselves as leaders in the realm of precision manufacturing, ensuring their success in an increasingly competitive landscape.